Lors de la première vague de la pandémie du coronavirus, en mars 2020, le secteur de la fabrication additive s’est mobilisé pour venir en aide à un milieu médical en pénurie de matériel. Profitant de contraintes réglementaires moins strictes que celles appliquées à la santé, les professionnels de l’impression 3D ont imprimé en grandes quantités des masques à visières, des ouvre-portes, des valves de respirateurs, ou des écouvillons nasaux. Pourtant, comme bon nombre de secteurs d’activités, la fabrication additive a rencontré certaines difficultés. D’après le rapport Wohlers 2021, bien que l’industrie soit en croissance par rapport à 2020, elle était nettement inférieure à celle des années précédentes, 7,5 % contre une moyenne de 27,4 %. Cet éloignement prolongé de la production et de la vente, combinées à d’autres facteurs comme le ralentissement de marchés clefs de la fabrication additive (aérospatiale, dentisterie, automobile…) a fortement impacté les revenus générés par la vente d’imprimantes 3D. Toutefois, le marché a atteint 12,8 milliards en 2020.
Enfin, une enquête sur le nombre de ventes d’imprimantes 3D a montré que, même si elles ont augmenté, en particulier pour les imprimantes 3D industrielles, les ventes sont encore à la traîne en 2021 par rapport à 2019, année somme toute morose pour la fabrication additive. Selon certains experts, le ralentissement observé depuis le début de la pandémie serait lié à un marché de l’automobile atone, un secteur manufacturier fragile et à des économies atones. Ceci expliquant, en partie, les résultats d’une étude menée par Context qui montre que ce sont surtout les ventes d’imprimantes 3D industrielles qui ont diminué sur la période. A contrario, et de manière surprenante, le marché de l’imprimante 3D grand public a vu ses ventes augmenter de 18 % en 2020, par suite des confinements.
Malgré un marché en dents de scie, quelques entreprises ont tout de même réussi de jolies levées de fonds depuis 2019. L’entreprise californienne Relativity Space, spécialisée dans la fabrication de moteurs de fusées par impression 3D a levé, depuis sa création en 2016, plus de 1,3 milliard de dollars dont 650 millions en juin 2021. La société américaine Carbon, spécialisée dans la fabrication additive de résine, est également en tête du palmarès des levées de fonds des dernières années. Avec un total de 682 millions de dollars, dont plus de 260 M$ en 2019. L’entreprise de construction ICON, dédiée à la fabrication additive béton pour la construction et l’aménagement de logements, a également levé d’importantes sommes d’argent ces derniers mois : 266,5 millions de dollars pour un total de 6 tours de financement, dont 5 depuis janvier 2020. Les exemples ne manquent pas. Enfin, alors que les spécialistes envisageaient une consolidation du marché en 2021, ils ont dû revoir leurs prévisions puisque le rythme de consolidation n’a pas été aussi rapide que prévu.
Qu’est-ce que la fabrication additive ?
Définition
Contrairement à la fabrication soustractive (appelée aussi usinage) — dans laquelle de la matière est retirée jusqu’à obtenir la pièce désirée — la fabrication additive — ou impression 3D — construit les pièces par ajout de matière. L’addition se fait par couches successives déposées sur la précédente et liées à celle-ci. Ce procédé de fabrication d’une pièce part d’un fichier numérique en 3D qui est directement converti en une pièce usinée.
Plus précisément, le processus de fabrication se décompose en plusieurs étapes :
– un fichier CAO du modèle tridimensionnel de la pièce est réalisé,
– un logiciel permet de « découper » l’objet 3D en une multitude de couches
– un paramétrage logiciel spécifique transforme la géométrie décrite dans le fichier en un ensemble d’instructions-machine (intensité du laser, vitesse de la tête d’impression, trajectoire, etc.). – ces instructions sont passées à la machine, qui les utilise pour imprimer la pièce souhaitée. Pour finir, des post-traitements peuvent être réalisés sur la pièce si besoin (traitement thermique, polissage, etc.).
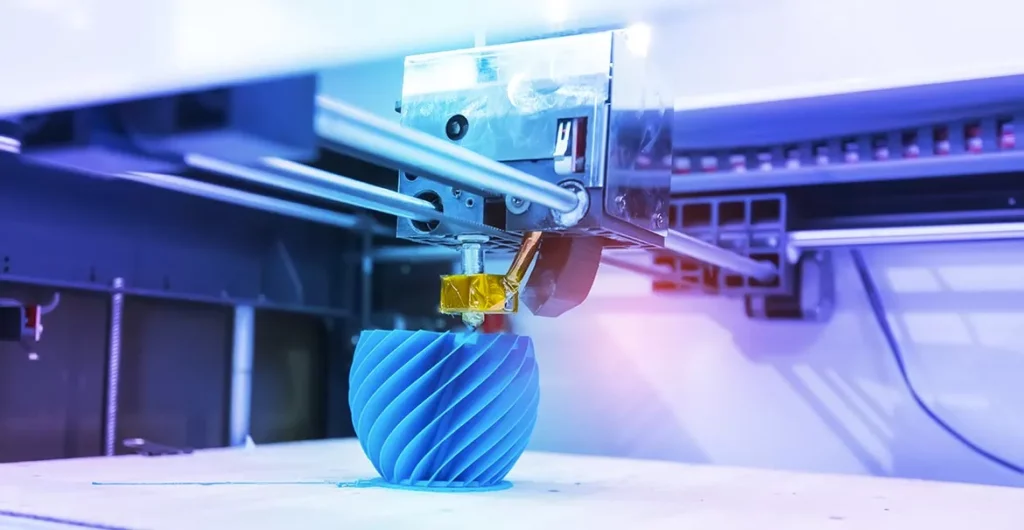
Les procédés
L’une des grandes forces de l’impression 3D réside dans la multiplicité des procédés. Selon la norme ISO 17296-2, il existerait sept grandes familles de procédés de fabrication additive dont les caractéristiques sont différentes :
- L’extrusion de matériel (FDM pour Fused Deposition Modeling)
Ce procédé consiste à déposer de la matière (liquide ou semi-liquide) via une tête d’impression. La matière passera à l’état solide une fois déposée. On construit donc un objet en superposant des traits solidifiés couche par-dessus couches. Ce procédé est le plus répandu, car le plus simple et peu dangereux. On le retrouve dans les imprimantes personnelles.
2. Photopolymérisation en cuve
Ce procédé regroupe la Stéréolitographie (SLA), le Digital Light Processing (DLP) et le Continuous Liquid Interface Production (CLIP). Le principe est d’utiliser une résine contenue dans un bassin et une source de lumière pour solidifier ladite résine. La photopolymérisation est particulièrement utilisée dans l’industrie dentaire, pour les objets d’art (joaillerie, figurine, etc.) ou pour des prototypes ou pièces de remplacement qui demandent un haut niveau de précision.
3. La fusion de bain de poudre (Powder bed fusion)
Ce procédé débute avec un bain de poudre, qu’on va faire fondre de manière sélective en utilisant un faisceau d’énergie (laser, électron). Le processus permet d’obtenir des pièces de très haute précision, tant en métal qu’en plastique, de bonne tolérance et avec d’excellentes propriétés mécaniques, mais à un coût élevé.
4. Le jet de liants (Binder jetting)
Ce procédé utilise deux matériaux : un bain de poudre et un liant. On dépose une fine couche de poudre en strate et on la lie sélectivement grâce à un jet de liant (similaire à une imprimante à jet d’encre). Le liant peut être chauffé dans certains cas pour améliorer l’adhésion ou cuit dans une phase de post-traitement.
5. Le jet de matériel (Material Jetting)
Le principe est de projeter sélectivement un jet de résine (ou autre matériel de fabrication) qu’on va aussitôt solidifier grâce à de la lumière ou un laser. Le jet de matériel permet d’obtenir des objets avec un beau fini et de bonnes tolérances, en plus de permettre de facilement varier les couleurs ou même les matériaux à l’intérieur d’un même objet.
6. Dépôt d’énergie dirigé (Directed Energy Deposition)
Comme pour la soudure, on dépose de la matière première à l’état solide et on utilise un faisceau d’énergie (laser, électron) pour la faire fondre au fur et à mesure qu’elle est déposée. Ce procédé permet, entre autres, de réparer des objets métalliques (ex. : pales de turbine) et de fabriquer des pièces de très grand format.
7. Stratification (Sheet lamination)
Ce processus consiste à superposer des feuilles et à les joindre (par ultrason dans le cas du métal ou grâce à des liants pour les plastiques). Dès qu’une feuille est liée, elle est découpée afin de représenter la forme 3D. On finit par former un objet en 3D en superposant ces feuilles les unes sur les autres.
Les principaux matériaux utilisés en fabrication additive
La démocratisation de la fabrication additive et la pénétration rapide de cette technologie dans de nombreux secteurs d’activités sont permises par l’extrême adaptabilité du process. Parmi les avantages indéniables de la fabrication additive (sur les autres processus de fabrication), la gamme de matériaux pouvant être utilisés ne cesse de progresser jour après jour. Le processus de sélection des matériaux nécessite un compromis qui inclut un certain nombre de facteurs à prendre en compte et à comparer. Parmi ces éléments, on peut citer l’application, la fonction, la stabilité, la durabilité, l’esthétique, le budget et les priorités du concepteur.
Les polymères
Les plastiques et les polymères sont actuellement les matériaux les plus couramment utilisés, principalement pour leur praticité, leur légèreté et leur prix. Il existe huit grandes familles de polymères dont les trois suivants sont les plus utilisés :
- – L’acrylonitrile butadiène styrène (ABS) est le plastique le plus répandu dans les applications de production par impression 3D. Il est solide, durable et peu coûteux.
- – Le polyamide (PA), ou « nylon » est plus résistant que l’ABS, mais il coûte plus cher. Il possède un grand nombre de propriétés physiques, notamment une robustesse et une ductilité (la capacité d’un matériau à se déformer plastiquement sans se rompre) importantes, qui en font un matériau de choix pour les prototypes fonctionnels.
- – Le polycarbonate (PC) est un polymère léger et dense, avec une bonne résistance à la traction. Il est également très résistant aux chocs. Lorsqu’il est renforcé de fibres, il peut être utilisé pour imprimer des pièces d’une rigidité et d’une résistance exceptionnelles.
Les polymères offrent une étendue d’usages très large aux industriels. Pour autant, ces matériaux doivent présenter un certain nombre de caractéristiques répondant aux besoins de toutes les parties, dont ceux des utilisateurs finaux. Les propriétés les plus demandées sont :
- – La stabilité mécanique. Le matériau ne doit pas se déformer durant l’ensemble du processus de fabrication, mais également après. Elle définit la durée de vie du produit, permet sa manipulation et offre les mêmes propriétés que les matériaux traités de manière conventionnelle (par moulage par injection).
- – La stabilité chimique. Le matériau doit avoir une structure chimique cohérente. Il doit être inerte lorsqu’il est en contact avec d’autres matériaux pendant et après le traitement.
- – La stabilité thermique. Le matériau doit avoir des propriétés (indice de fusion, taille des particules, adhérence, etc.) requises pour les processus de fabrication additive choisis. Il doit également posséder des propriétés thermiques (température de transition vitreuse, résistance au fluage, résistance aux basses et hautes températures, etc.) requises pour l’application finale.
- – La biocompatibilité. Certaines applications (médicales, dentaires, biologiques) nécessitent une biocomptabilité afin d’éviter tout rejet. De même, cette propriété est essentielle pour les pièces destinées à être recyclées. La toxicité doit alors tendre vers 0 et, si possible, être biodégradable.
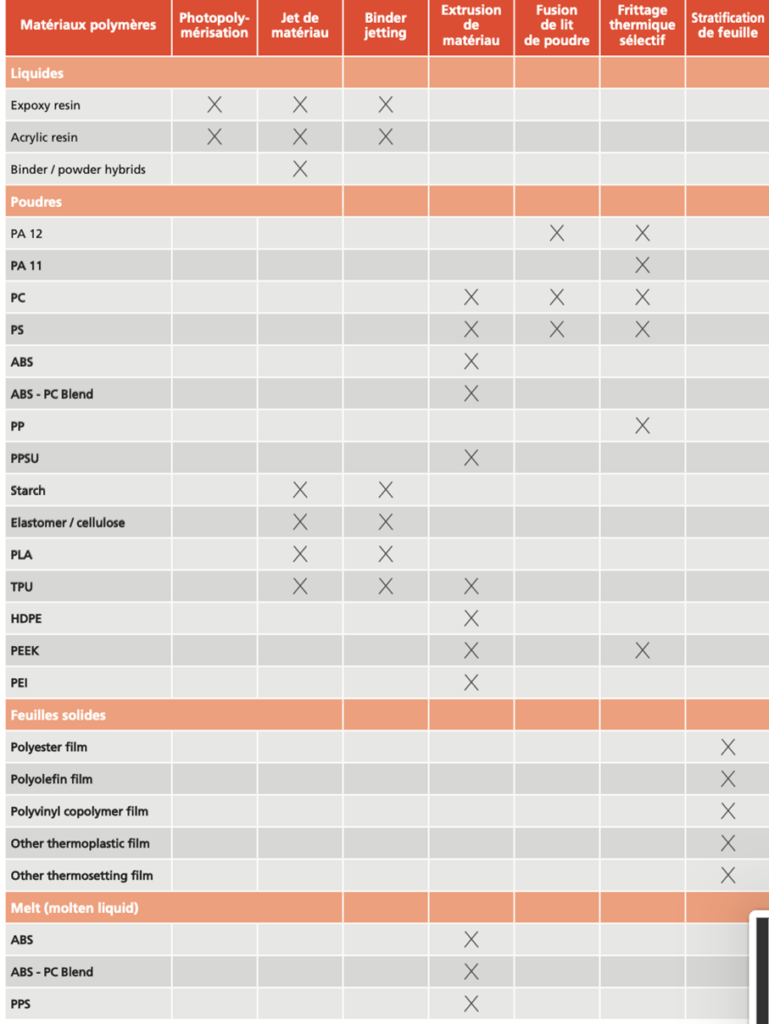
Les métaux
L’étude de 2020 diligentée par Wohlers montre que l’impression 3D métal arrive en 4e position derrière les photopolymères, les poudres polymères et les filaments avec 17 % de part de marché. Une étude plus ancienne de l’Observatoire de la métallurgie, réalisé en 2018, estimait à 60,6 M€ le marché de la fabrication additive métallique français. Les métaux les plus utilisés sont généralement l’acier, le titane et l’aluminium, chacun ayant des propriétés propres.
• L’acier est un matériau très abordable en termes de coût. Il est utilisé dans des environnements à haute pression et haute température, dans lesquels le poids n’est pas une préoccupation. Il peut être inoxydable.
• Le titane est un métal léger, résistant et biocompatible. Il est particulièrement apprécié pour les applications aéronautiques et spatiales, mais aussi médicales.
• L’aluminium n’est pas aussi solide que l’acier ou le titane, mais il est plus résistant à la corrosion. Il est également léger et polyvalent, ce qui le rend idéal pour le secteur automobile. Enfin, il offre la possibilité de créer des pièces avec des détails fins.
Les céramiques
La céramique, l’un des plus vieux matériaux utilisés par les hommes, se prête parfaitement bien à la fabrication additive. Il existe plusieurs types de céramique sur le marché comme les carbures, les oxydes (d’aluminium et de zirconium), les nitrures, les céramiques silicatées.
Comme pour les polymères et le métal, les procédés d’impression sont variés (voir schéma ci-dessous). La diversité des propriétés va de la résistance à l’usure et à la chaleur, de la résistance à la température et à la corrosion en passant par la biocompatibilité et la compatibilité alimentaire. Sa légèreté, combinée à sa capacité à supporter les chaleurs extrêmes sans se déformer en fait un candidat idéal pour les applications à très hautes températures. Ces multiples propriétés permettent d’utiliser les céramiques techniques dans une variété d’applications en industrie automobile, électronique, technologie médicale, énergie et environnement et en général ingénierie en équipement et génie mécanique.
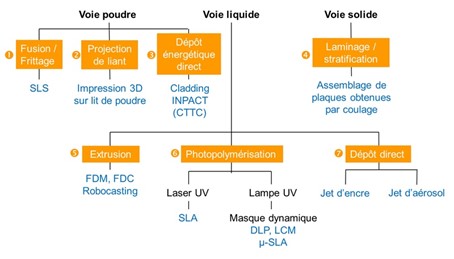
Le cabinet d’études IDTechEx a publié un nouveau rapport sur le marché de la fabrication additive céramique : celui-ci devrait représenter une valeur de 400 millions de dollars d’ici 2032, soit 7 fois plus qu’aujourd’hui.
Les matériaux composites
Les matériaux composites sont fabriqués à partir de deux matériaux offrant des propriétés physiques complémentaires. L’un est le « liant » qui entoure et lie les fibres ou les fragments de l’autre matériau, qu’on appelle le « renforcement ». On les retrouve, par exemple, dans l’outillage ou dans la fabrication de pièces fonctionnelles. Parmi les matériaux composites les plus populaires, on trouve ceux renforcés de fibres de carbone ou de fibres de verre. La gamme des composites est en expansion constante. Le plus grand avantage des matériaux composites modernes est qu’ils sont à la fois légers et solides.
Deux grands usages : prototypage/outillage et production
La fabrication additive ouvre les portes à deux voies. Cette technologie est en effet utilisée à des fins : de prototypage/outillage et de production en série.
Le prototypage, premier débouché de l’impression 3D
Historiquement et pour des raisons liées à l’évolution de la technologie, les premiers débouchés de l’impression 3D se concentraient sur le prototypage rapide. Les ingénieurs dessinaient une maquette 3D puis imprimaient un prototype. À partir de celui-ci, on réalisait une maquette ou un moule puis on coulait la pièce en utilisant des techniques d’usinage classiques. L’avantage du prototypage rapide et du recours à l’impression 3D pour le réaliser peut s’énoncer en trois points :
– le temps : par l’agilité permise par la mise en œuvre de la fabrication additive, le gain de temps au niveau du développement de produits est substantiel ;
– le coût : le prototypage rapide permet de réaliser des prototypes sans qu’il soit nécessaire de recourir à des outillages coûteux, tout en garantissant les performances du produit final. Le coût environnemental est également réduit lorsque l’on a recours à la fabrication additive puisque cette méthode utilise la quantité de matière nécessaire à la pièce contrairement à la fabrication soustractive qui part d’un bloc pour en retirer des éléments lors de l’usinage.
– la complexité des formes : l’un des atouts de la fabrication additive est de permettre de tester des formes complexes impossibles à obtenir avec les procédés classiques. La gamme de prototypage en est alors élargie.
C’est à cette problématique que répond Fab’Innov, start-up bordelaise accompagnée par Unitec. L’entreprise propose deux services : celui de la conception 3D de pièce et celui de prototypage de ces mêmes pièces. Elle intervient dans quatre grands secteurs d’activités : le design, l’architecture, la santé et le secteur industriel. Elle accompagne les entreprises désireuses de prototyper des pièces dans le choix des matériaux et des techniques pour valider leurs projets.
L’usage de la fabrication additive dans le secteur de l’outillage
Autre domaine dans lequel on retrouve la fabrication additive est celui de l’outillage. En effet, de plus en plus, cette activité essentielle a tendance à s’horizontaliser et à s’internaliser : des outils de fabrication appropriés et efficaces augmentent l’efficacité et la rentabilité de l’entreprise. Les applications en fabrication additive pour l’outillage couvrent une large gamme d’utilisations, y compris pour les outillages utilisés dans les procédés de coulée et d’usinage, les gabarits d’assemblage et les fixations, ainsi que les guides médicaux personnalisés. Le recours à l’impression 3D permet aussi aux entreprises d’être beaucoup plus agiles et de ne plus dépendre des fournisseurs d’outillages. Cela entraine une réactivité qui est synonyme de réduction des coûts de production et une accélération de la mise sur le marché des produits finis. Cette technologie est particulièrement attrayante pour les professionnels de la fonderie.
La fabrication additive est également exploitée pour la fabrication de moules de haute précision aux formes sophistiquées, qu’il s’agisse de moules pour l’injection plastique, très utilisés parmi les sous-traitants automobiles, de moules ou noyaux en sable pour la fonderie, en cire pour la joaillerie ou encore de moules métalliques pour la fabrication de pneus. Cette technique déjà assez répandue offre des gains de l’ordre de 30 % à 40 % sur le temps de refroidissement de la pièce injectée.
Production
Toujours d’après le rapport Wohlers 2020, la fabrication additive pour la production de série convainc de plus en plus d’industries qui ont désormais recours à cette technologie pour produire des pièces en grand nombre. Selon le rapport, $1,40 milliard de dollars ont été dépensés dans la production de pièces finies imprimées en 3D dans le monde.
Les avantages sont toujours les mêmes : gain de temps, liberté de conception, possibilités nouvelles, économies, gains de matière et respect de l’environnement. Cependant, comme le souligne un Rapport sur la Fabrication additive réalisé par La Fabrique en 2016, il existe encore et toujours de nombreux freins (qui depuis ont tout de même diminué) : un coût des machines (imprimantes 3D) et des matériaux encore élevé pour bon nombre d’entreprises. Même si les nouvelles imprimantes permettent une augmentation de la taille et du volume des pièces produites, la fabrication additive ne peut, à ce jour, répondre à des demandes de pièces de très grand gabarit.
Continuer la lecture vers la partie 2 « L’ORGANISATION DU MARCHÉ »